Oil Gas (Production)
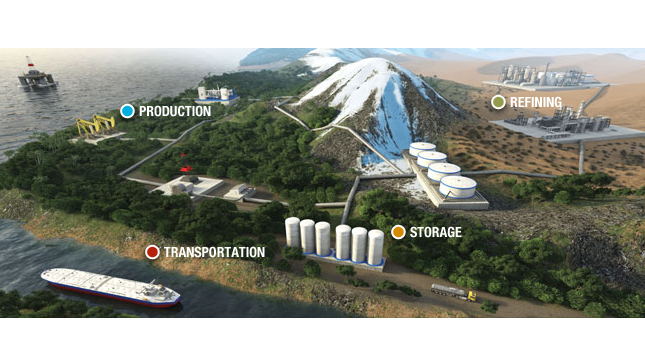
Production Overview
Safety‚ uptime and efficiency: the key operating metrics that your performance is measured on for all onshore and offshore production facilities. Remote locations‚ a limited number of operators and extreme climates: the difficulties you face every day in meeting your goals and objectives. CIRCOR knows and relates to the needs of facility managers in the upstream sector and offers safe and reliable fluid-handling solutions that allow you to focus on running your operations.
Onshore And Offshore Expertise
CIRCOR has proven experience in these challenging Production applications‚ whether on the open water or on land:
- Field Gathering Pumps
- Heater Treater Charge Pumps
- Free Water Knockout Pumps
- Desalter Bottoms Pumps
- Multiphase Pumps
Heater Transfer Charge
After exiting the Free Water Knockout (FWKO) system‚ the partially dehydrated oil-water emulsion is fed into the Heater Treater process by charge pumps. The Heater Treater system consists of a pressurized vessel‚ or a series of pressurized vessels‚ in which a bottom-mounted heat source is operated‚ fueled typically by natural gas. The incoming well-mixed oil-water emulsion is heated by means of its direct contact with the aforementioned heat source. The ensuing temperature increase reduces the molecular attraction between the oil and water molecules‚ permitting the water droplets to settle out more rapidly. To increase the efficiency of this process‚ other mechanical and gravity separation methods are often employed. To provide adequate time for effective separation of the oil and water‚ a longer retention time is required within this upstream system. The dehydrated crude is then delivered under pressure to the desalter system.
As experience bears out‚ Heater Treater Charge processes have their challenges. The basic operation of the system is designed around reasonably steady-state production conditions. In reality these seldom happen. Both high and low flow rates adversely impact the ability of the oil-water emulsion to effectively separate. Similarly the incoming crude at times has not been suitably de-watered‚ which demands additional energy to heat the fluid‚ due to the increased volume of water and its greater heat capacity as compared to oil. From a charge pump standpoint‚ the fluids being managed are highly viscous emulsions. They are typically being delivered under very challenging and dynamic suction conditions‚ due to the frictional losses between the outlet of the FWKO system and the inlet to the Heater Treater system and varying production demands.
Suitable Pump Types:
Field Gathering
The routing of the raw‚ unprocessed crude oil from the wells to the main storage facility‚ processing plant or shipping point is managed by the Field Gathering network. There are two types of gathering systems: radial and trunk line. The radial type brings all the flowlines to a central header‚ while the trunk-line type uses several remote headers to collect fluid. The latter is mainly used in large fields. The pipelines that comprise a Field Gathering network are usually smaller in nominal diameter and overall length as compared to high-flow‚ cross-country shipping pipelines‚ with the oil being transported typically containing higher percentages of sand‚ water and/or evolved gas. Depending on the distance between the production wells and the upstream delivery point‚ and the viscosity and composition of the fluid being managed‚ a reasonable pressure boost from the Field Gathering line pumps may be demanded to overcome the friction losses.
As experience bears out‚ Field Gathering systems have their challenges. The crude oil managed by the Field Gathering pumps is often times contaminated with solids‚ produced water‚ salts and waxes‚ typically requiring blending with condensates to stay with the maximum allowable working pressure limits of the gathering lines. The remote locations of the gathering line booster stations demand highly dependable equipment that can support operation at a wide range of flow rates‚ due to the changing output from the field. Also‚ the pumping solutions selected must be efficient since electrical power must be generated locally at a premium.
Suitable Pump Types:
Free Water Knockout
After leaving the first stage vertical separator‚ the high pressure liquid portion of the produced fluid stream is directed towards the FWKO pressure vessel. This long‚ horizontal device is used to separate free water from degassed crude oil and crude oil-water emulsions‚ due to the differences in the densities of these mediums. Depending on the distance to this device‚ which is normally located at the Central Processing Facility‚ pumping may be required to boost the liquid to the inlet connection of this vessel. As the liquid enters the vessel the design residence time allows a large portion of the water to separate from the crude‚ collecting in the lower portion of the vessel. The captured water is pumped away for ultimate re-use in water flooding re-injection. The partially processed oil is now available for forwarding to the Heater Treater system.
As experience bears out‚ FWKO processes have their challenges. The basic operation of the system is designed around reasonably steady-state production conditions. In reality these seldom happen. Both high and low flow rates adversely impact the ability of the crude oil and water to effectively separate. Similarly the incoming crude at times has not been suitably degassed‚ so undesirable free gas is carried through the entire process. To minimize the vessel size and the elevation above grade‚ the FWKO pumps typically have very difficult suction conditions. When you factor in the inevitable presence of solid particulates‚ waxes‚ paraffins and even H2S in the process fluid‚ the pumps in this system face very demanding services every day.
Suitable Pump Types:
Desalter Bottoms
After leaving the Heater Treater system the dehydrated crude is delivered to the pressurized Desalter vessel‚ in which harmful contaminants like salt‚ clay‚ silt‚ rust and other debris are removed. It is critical that these undesirable reservoir residues are extracted from crude oil to avoid costly corrosion and fouling of downstream equipment.
Over time‚ these separated solids will accumulate in the bottom of the Desalter vessel; hence‚ the Desalter must be periodically washed to remove this accumulation. To handle this cleaning operation‚ a “mud washing” system is installed in the bottom of the vessel to periodically remove the solids. Mud washing consists of recycling a portion of the Desalter effluent to agitate the accumulated solids so that they are washed out. These solids are then routed to the wastewater system. In both services pumps are required.
The operation of a desalting system can be very challenging‚ due to changing process variables. At best‚ it is a process of measuring trade-offs and compromises. A delicate balance must be maintained while controlling mixing intensity and feed levels to provide optimal salt removal. The fluid-handling equipment supporting the Desalter must be reliable and robust enough to withstand aggressive levels of corrosive and abrasive wear‚ as well as the arduous start and stop cycling of this intermittent duty.